Troubleshooting & FAQs
Some common FAQs and troubleshooting questions are answered below. If you experience an issue that is not covered here, or if the suggested actions do not resolve the problem, please contact our Customer Success Team for more help.
Latest Updates: Take advantage of new features, and the latest bug fixes by ensuring you have installed the latest;
Software: Lab Software
Firmware: Firmware Update Process
Frequently Asked Questions
Note: Performing a Hard Reset of Your Device
Many common failure modes can be resolved by performing a hard reset of the device. This is achieved by holding down the button for 10-30 seconds or until the LEDs light up. The initial button press/hold will cause the LEDs to indicate current battery life. Continue holding down the button until the LEDs light up and then let go. This will not delete any data on the unit or change the configuration, it just reboots it.
Hardware
How many sensors are in an enDAQ and how accurate are they?
- Main triaxial accelerometer
- Secondary triaxial accelerometer (not available on -D40 and -D16 variants)
- Orientation sensor
- Gyroscope
- Temperature
- Pressure
- Humidity
- Light
- Microphone - only on W
- GPS - only on W
There are typically 2 triaxial accelerometers, 2 temperature, 2 pressure, humidity, light, and an orientation (gyroscope or quaternions) sensor. More information on the specific sensors (including the actual part number of the sensor) is available in our Embedded Sensor Specifications article.
How long does the battery last?
Our battery life estimator tool can help you determine how long the battery will last based on your desired configuration settings. This calculator assumes room temperature conditions and a relatively new device. Battery life may vary based on environment and device condition. Our battery specifications article provides more details on the batteries we use and what factors may impact your battery life.
How accurate is the enDAQ sensor?
This is a little more difficult to answer than one may expect. An accelerometer will have different specifications that will affect "accuracy." These include noise, resolution, non-linearity, temperature sensitivity, and frequency response. But frequency response has the highest impact; so as long as the frequency of the vibration is within the rated range for the specific sensor the device should be within 5%. On the piezoelectric accelerometer there will be a low-frequency negative error. And on all accelerometers as the frequency approaches resonances (either within the sensor, or due to case construction). All internal accuracies get trumped however by mounting. If the device (or any accelerometer) is not mounted correctly you can experience grossly wrong results. We wrote a blog on mounting that provides more insight on this impact on accuracy.
Detail
The tables in our Embedded Sensor Specifications article provide the broadband noise levels of the accelerometers; but some users are also interested in the noise vs frequency level. The following three plots are FFTs of each of the main accelerometer types when recording in our sensor. There are some frequencies that will appear in the FFT because of the noise from the accelerometer and/or sampling electronics and are not characteristics of your vibration/shock environment.
ADXL
An FFT of the ADXL345 (digital capacitive accelerometer) shows relatively good/low broadband noise levels. There is a noticeable spike around 25 Hz that appears inherent to the digital component. This data is with a sample rate of 200 Hz, a higher sample rate will see harmonics of this 25 Hz frequency component repeating at a similar level of ~0.001g.
3255A
Data from the 3255A accelerometer (piezoresistive accelerometer) is shown. There is known frequency around 25 Hz, and then the harmonics, in every component/axis that is a result of the on-board programmable gate array doing the temperature compensation. It’s a characteristic of this accelerometer.
832M1
The piezoelectric accelerometer has no inherent noise issues; but the enDAQ sensor's electronics introduces a small amount of noise when saving to disk. This frequency is about 1/4000 th of the sampling frequency. Midé is hoping to improve this in future releases.
When the battery is about to die and the device shuts down, will it save the data?
Yes, the sensor has a lot of protections and checks in place to sense the battery voltage dropping and will then close out the file beforehand. That being said, there are occasions where the battery voltage will drop too quickly and the file may not get closed out. This can result in a corrupt file that often can be fixed by Mide if need be. To help mitigate this, we recommend using recording limits and re-trigger mode to be continually closing files and creating new ones through a particularly long test.
Can the battery be replaced?
The batteries in our S2, S3, and S4 models cannot be replaced because the bottom volume of the recorder is potted with an epoxy to mechanically stiffen the assembly and directly couple the accelerometers with the bottom of the enclosure. This potting extends into the volume where the battery is located so it cannot be replaced.
The S5 models have a different battery and battery location so the battery can be replaced in these units.
Please note that all of our models can operate while plugged into power so, if you have a model with a battery that cannot be replaced, your device will not be completely useless.
Do keep in mind that depending on use, charge cycles, temperature etc. the battery lifetime is 2 to 3 years.
What happens when a piezoelectric accelerometer experiences an acceleration level outside its measurement range?
This can cause the charge amplifier within the accelerometer to saturate which will result in a logarithmic decay following the event. Our blog on piezoelectric accelerometers goes into more detail on why this happens. Sometimes this occurs because of high-frequency vibrations which can excite resonances inside the accelerometer. In this case, you may need some mechanical damping. The piezoresistive accelerometers are the best for shock testing however as they do not experience this issue and even have internal gas damping to prevent resonance issues. PCB Piezotronics also has a nice application note with more information on this "issue" with piezoelectric accelerometers. Below is an image showing some data captured by two different devices with piezoelectric and piezoresistive accelerometers to show the difference.
Software
Are there any example files to download to help evaluate the software and products?
Yes! We've sold over 15,000 data recorders that have generated many, many recordings. You can find some test data and sample recordings here.
Lab
enDAQ Lab Software does not Run
This is likely due to a security issue; you may have to contact your IT department. You may need to change your apps settings in Microsoft to allow you to run apps from "anywhere" as shown if you receive an alert that the software wasn't downloaded from the Microsoft Store. This error is due in part to the fact that enDAQ Lab does not have an installer. It is a “portable” application, which can simply be copied to and run from anywhere: external disks, flash drives, recorders, etc. Lastly as a reminder that currently, the enDAQ Lab only runs on Windows computers.
How do I download and install the Lab Software?
enDAQ Lab is completely free, all that is required is to complete a simple form that will ask for your email address and your test experience. Here is the link to download online here. The current release of the software requires a 64-bit version of Microsoft Windows.
Once downloaded, the software is completely self-contained; it requires no installation. Just double-click the executable and away you go! If you are evaluating the products and software, be sure to download an example recording file to help give you a chance to explore.
How do I export and convert data to MATLAB or other analysis software from enDAQ Lab?
enDAQ and Slam Stick devices record data in enDAQ's custom file format, a format designed to completely self-describe the device and the data within it. This article provides an overview on how to use the software to convert IDE files to MAT and other file formats such as TXT and CSV.
Another option is our enDAQ Analyzer software which is written in MATLAB. This software converts IDE files to a MAT format and then performs some analysis on the files. More information is available here.
What is the current version of the Lab software?
The most up-to-date release version is listed on the download page. There are typically 4 new software releases a year.
Troubleshooting
Why does the enDAQ measure +1g at rest, shouldn't it be -1g?
This is a good question and caused some initial panic internally at Mide when we first introduced units with the DC accelerometer. It's very counter-intuitive at first but let's try and explain it! The short answer is that accelerometers measure a deviation in acceleration from free-fall. So at rest, there is +1g acting upward to keep it still and overcome Earth's gravitational acceleration downward.
Accelerometers have a suspended proof mass and they measure the strain on springs holding that proof mass. When the device is on your desk the proof mass isn't perfectly centered so it can see that shift in location. When in free fall the proof mass becomes centered and therefore it measures 0g acceleration... at least that's how I've explained it to myself. There's a bit more formal of an answer related to Einstein's "equivalence principle." Below is an excerpt from Wikipedia that has a bit more information.
An accelerometer measures proper acceleration, which is the acceleration it experiences relative to freefall and is the acceleration felt by people and objects.[2] Put another way, at any point in spacetime the equivalence principle guarantees the existence of a local inertial frame, and an accelerometer measures the acceleration relative to that frame.[3] Such accelerations are popularly denoted g-force; i.e., in comparison to standard gravity.
An accelerometer at rest relative to the Earth's surface will indicate approximately 1 g upwards, because any point on the Earth's surface is accelerating upwards relative to the local inertial frame (the frame of a freely falling object near the surface). To obtain the acceleration due to motion with respect to the Earth, this "gravity offset" must be subtracted and corrections made for effects caused by the Earth's rotation relative to the inertial frame.
The reason for the appearance of a gravitational offset is Einstein's equivalence principle,[4] which states that the effects of gravity on an object are indistinguishable from acceleration. When held fixed in a gravitational field by, for example, applying a ground reaction force or an equivalent upward thrust, the reference frame for an accelerometer (its own casing) accelerates upwards with respect to a free-falling reference frame. The effects of this acceleration are indistinguishable from any other acceleration experienced by the instrument, so that an accelerometer cannot detect the difference between sitting in a rocket on the launch pad, and being in the same rocket in deep space while it uses its engines to accelerate at 1 g. For similar reasons, an accelerometer will read zero during any type of free fall. This includes use in a coasting spaceship in deep space far from any mass, a spaceship orbiting the Earth, an airplane in a parabolic "zero-g" arc, or any free-fall in vacuum. Another example is free-fall at a sufficiently high altitude that atmospheric effects can be neglected.
The Device Appears “Frozen” and is Unresponsive
If the unit is not responding to button presses and/or displays a constant LED indication (even when unplugged from power) the software is hanging up. Try performing a hard reset of the device. This is achieved by holding down the button for 10-30 seconds or until the LEDs light up. The initial button press/hold will cause the LEDs to indicate current battery life. Continue holding down the button until the LEDs light up and then let go. This will not delete any data on the unit or change the configuration, it just reboots it.
No LED Activity after Pressing the Button
This may be due to the battery being depleted and therefore the device requires charging. Also try a hard reset by holding down the button for 10 seconds. If this doesn’t resolve the issue, contact Midé for assistance.
There are No New Recording Files on the Device
This question comes up often. Remember the device will never start recording or looking for a trigger until the button is pressed regardless of the trigger configuration. Another possible explanation is that the trigger conditions were never met. Also, check to ensure there is storage space available on the device (it appears as a standard USB flash drive). The battery could have also died that prevented the unit from recording. Finally, make sure to read the Recording File Naming & File Structure Section to understand how files are named and stored on the device. If the problem persists, contact Midé for assistance.
Data File is Corrupted or Does Not Display Data
The device may have suddenly run out of power and therefore did not close out the file properly. This can happen rarely due to battery dips; but can also happen from sudden and extreme impact events directly to the device, water damage, and rapid temperature swings. When the file is corrupt you may not be able to open it, or it is more likely that the file will open but only display a few seconds worth of data even though the file should have minutes or even hours. Unfortunately, this means that the few seconds of data are being repeated throughout the file due to the corruption.
There are a couple of ways to prevent this from happening in the future:
- Update your firmware - we are always adding more functionality to try and handle this condition better. See here for more information.
- Record for shorter time periods and retrigger - this will ensure that if there is a corruption again, it only affects the last file in your test; not the full duration. We'd recommend setting 15-minute recording intervals with a 1-second delay, then re-trigger. See here for more information.
- Connect to external power - the battery may be older and/or the temperature range may be making it especially susceptible to failure. We'd recommend using an external power source if this is the case.
- You may need a new unit - the battery is, unfortunately, a primary driver of failure. Rechargeable batteries age with time, temperature, and usage. It may be time to replace the device. See here for more information on battery age.
The Device does not appear in “My Computer” when Connected
Wait several moments to ensure that the computer isn’t first trying to “recognize” the device. Then try to ensure that the USB cable is properly connected; the blue LED should turn on when connected to the computer. You’ll also want to ensure that the USB cord you are using is capable of transmitting data and not just meant for charging. Also, the device won’t properly connect when it is still in the recording or trigger mode. One other possibility is that your computer’s security software is blocking the device; please try a different computer and/or contact your IT department.
enDAQ Lab Software does not Run
This is likely due to a security issue; you may have to contact your IT department. You may need to change your apps settings in Microsoft to allow you to run apps from "anywhere" as shown if you receive an alert that the software wasn't downloaded from the Microsoft Store. This error is due in part to the fact that enDAQ Lab does not have an installer. It is a “portable” application, which can simply be copied to and run from anywhere: external disks, flash drives, recorders, etc. Lastly as a reminder that currently, the enDAQ Lab only runs on Windows computers.
I Work for the Navy and I need the Correct Configuration File
There is a specific configuration file recommended by NAVAIR for testing on F/A-18s that disables all sensors besides the pressure channels. It is attached here.
Microsoft Windows is Prompting to Scan and Fix the enDAQ (old Slam Stick) Drive
Some Windows versions present this dialog for some drives not formatted by Windows. This message is harmless; the user may either proceed with or cancel the scan.
When the Device Initially Plugs into Power, only the red LED Flashes
This indicates an error code. Take note of the number of times the LED flashes and reference the list of error codes.
Ordering & Quoting
When will my order ship?
All of our sensors are made to order to ensure the newest calibration date. Because of this, it takes about 1-2 business days for your order to ship if the materials are in stock.
How much will shipping cost?
The shipping is dependent upon your shipping location. The best way to determine your shipping costs is to place the desired products into our online shopping cart, proceed through the screen where address information is entered, and you can review various shipping options and costs before actually placing an order. We offer to ship via UPS to various locations around the world.
Can I use my own shipping account or service?
Some customers likely have their own FedEx, UPS, or DHL account that they prefer to use for shipping. If you would like to use your own account, please contact our Customer Success Team before placing your order and they can help you with this.
General FAQs
How do I select the right enDAQ sensor for my application?
There are 22 variants of enDAQ sensors so it can definitely be difficult to select the right one for you and your application! Our article on enDAQ Product Selection goes into more detail, but picking the right enDAQ sensor requires some estimation of what the environment is you're trying to measure. If you don't have a good idea, don't hesitate to reach out - but typically our enDAQ - 100g model is the most popular and versatile for general purpose testing.
What WiFi protocol do the enDAQ W units use?
They use the standard 2.4 GHz networks your phone and other devices use. A good check to know if you can use our W units is to see if your mobile phone has good signal strength to a 2.4 GHz network. Some WiFi networks now include an option for a 5 GHz network which our devices can not use. But typically there will be a 2.4 GHz available if there is a 5 GHz one available.
More specifically, the protocol is 802.11 b/g/n, and we support WPA and WPA2 security. Our wireless module is the ESP32 which provides even more detailed specifications online if needed.
Can the enDAQ W devices do any local wireless transmission?
Not right now, our devices will use a local WiFi network to connect directly to an AWS hosted cloud end point to upload data to. Then the cloud application processes that data upon upload into some summary metrics, and make it visible to your account that the device is paired to. But to access the data you will need to log into the cloud.
Mobile hotspots will work but be aware that iPhone has a power-saving feature to auto turn off the hotspot if no device has connected to it in the last 90 seconds ( see Apple support article). This can be very problematic with wireless enDAQ recorders because they only connect to WiFi when uploading. There is a workaround to keep the settings page open on your phone. But we will add some better support on the enDAQ device for working with mobile hotspots.
We recognize the need for more local wireless transmission to help mitigate any security concerns. Local wireless transmission will also allow our devices to "stream" packets of data in near real-time (less than 1 second). We will develop a USB dongle to plug into your computer which can act as a receiver to our wireless devices. This will mean our W units will in firmware (no need for a different product) allow the user to select for either cloud-based or local data streaming (if local, you would need to pair it to the dongle). This capability is in very early development and won't be available until 2024.
Why isn't the sample rate uniform in the file?
Why isn't the sample rate exactly as I define it in configuration?
We are "telling" the digital sensors to sample at a specific rate but their actual sample rate will deviate slightly based on a number of factors. Thankfully our system has an accurate and independent time clock so we are able to know and report/save the actual sampling rate reported.
Why does the sample rate "jitter" between data blocks?
The firmware grabs the data into blocks, records the start and end time of each block, and assumes evenly distributed sample times within the block. We have a 32 kHz clock used to capture timestamps which is a resolution of 30 microseconds. This forces us to round the start/end times of a block to +/-30 microseconds. From block to block this can make the timestamps look like they are "jittering" but this is purely an artifact of rounding when capturing the timestamps of blocks.
For example, let's say we get 2500 samples from time 0 to 0.5 seconds, and then 2500 samples between time 0.5002 (end of the last block + 1 sample time) and 1 second. But because of rounding, maybe the time gets recorded as being 0 to 0.49997, and then 0.50023 to 1.0000. Averaged across the blocks, the sample time within the block is insanely close to 5kHz. But from block to block this will look different.
Why does the sample rate change significantly for a long recording?
All the sensors/components have some degree of temperature sensitivity. This is true for the timing crystals used in the digital sensors too, and some are more sensitive than others. So the digital accelerometer will start recording faster/slower relative to the real time due to this change.
Thankfully our timing crystal we use to compute timestamps is very stable across temperature. So our timestamps reported are "real" for these macro changes across a long recording that has a large change in temperature.
What to do about this?
If your recording has a relatively stable temperature, you can/should assume a fixed sample rate across the entire recording and resample the data accordingly. And if you need the sample rate to be exactly 800 Hz you can use a built in function in scipy (https://docs.scipy.org/doc/scipy/reference/generated/scipy.signal.resample.html) or MATLAB to do that.
If you have a long recording with large temperature changes, We recommend splitting the file, then assuming the fixed sample rate in the splits which would be valid.
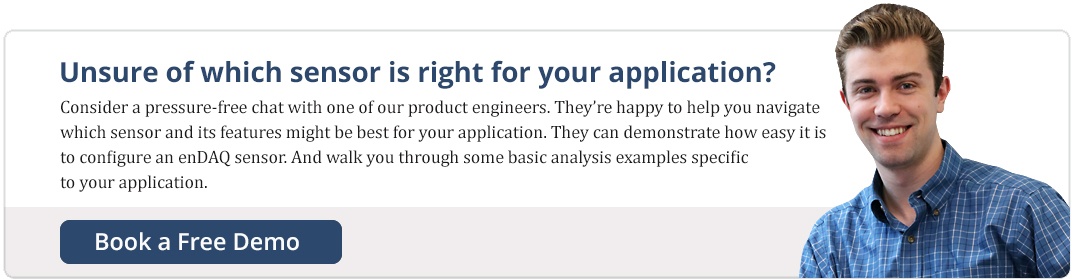